The manufacturing firm's digitisation drive is helping cut down inefficiencies
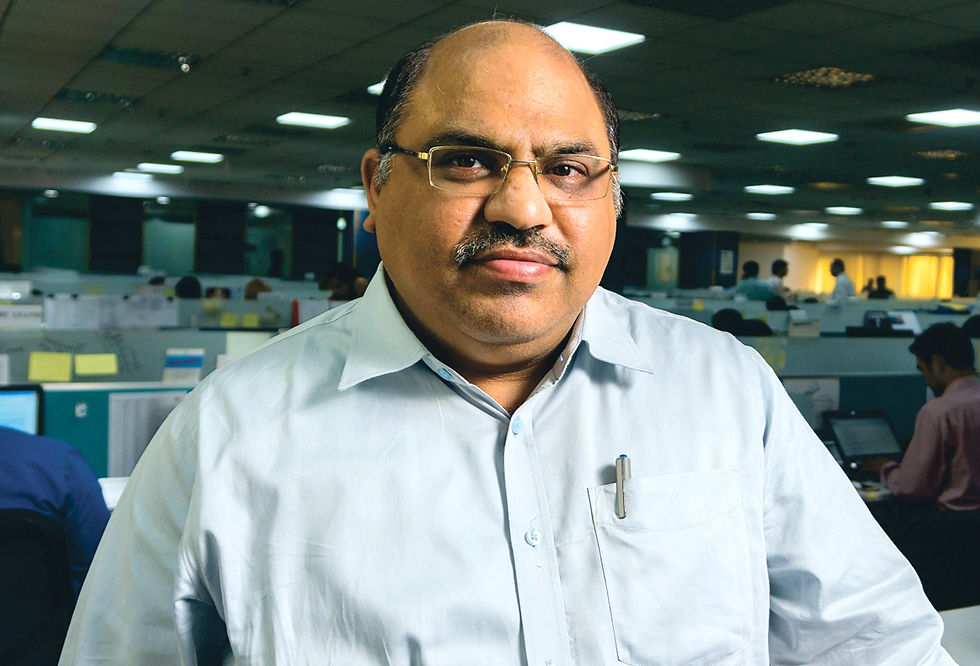
BIMAL PURI
SRF LIMITED
SRF is the first company in India to integrate the production machine data with ERP in the field of technical textiles. Multiple technologies like sensors, meters, wireless, Oracle ERP, barcode and middleware innovatively integrated to eliminate all manual work. This IT enablement has improved accuracy of production accounting while significantly improving manpower productivity and machine utilisation.
A CIO needs to synchronise himself with the business goals with a proactive mind instead of being reactive, feels Bimal Puri, CIO, SRF. And he is living by his words. Though SRF's journey started with a nylon tyre cord plant in Manali in 1970, the company, over the years, has not only expanded its product range under technical textiles but diversified into many related businesses. Besides technical textiles, today SRF's business profile constitutes fluorochemicals, specialty chemicals, engineering plastics and packaging films.
However, this growth and diversification came with its own set of challenges. SRF today has a workforce of around 6,500 of different nationalities working in 12 manufacturing plants in India, two in Thailand and two in South Africa. The company caters to customers spread over 75 countries. For SRF, despite having an ERP system, the shop-floor activities were controlled through manual log books which lead to inaccuracies of data, costing, genealogy and disconnect with ERP.
Moreover, the shop-floor productivity data of man and machine was not reliable to plan and take decisions. This was leading to duplicity of work and heavy manpower deployment of manpower on shop-floor which meant wastage of precious resources. “Lack of visibility of actual status of production was the key reason to this problem,” explains Puri. To fix these issues, the company had to improve shop-floor productivity and visibility. And this was done by automating and integrating machines with the ERP system already in place at SRF.
Next on Puri's agenda was to increase the accuracy of production accounting and actual costing of products. “We captured, analysed and improved the machine uptime and efficiency using analytics on this data,” says Puri. Thus, achieving machine and people productivity and operational excellence was the biggest achievement and biggest leap forward for SRF in its digital transformation journey.
Comentarios